1 Definition and application of ultra-thin glass
Ultra-thin glass refers to a thin glass sheet with a thickness of less than 1.3 mm, which has the characteristics of high light transmittance, high flatness, high precision and lightness, and has an extremely flat surface.
It can be used for TN/STN, TFT, OLED, TP and other flat panels Substrate glass and cover glass for displays are one of the key basic materials for the flat panel display industry.
2 Ultra-thin glass production process
Ultra-thin glass production process methods: overflow method, orifice down-draw method, flat drawing process, float process, etc.
Production process: raw material preparation→glass melting (including melting and pre-clarification)→clarification→forming→annealing→testing→cutting→cleaning→boxing and storage.
Ultra-thin glass production process
LCD substrate glass is divided into two categories: alkali-containing glass and alkali-free glass. Alkali-containing glass is mostly used in TN/STN-LCD, which is mainly produced by float process; alkali-free glass is used in TFT-LCD, which is mainly produced by overflow process.
Cover glass is mainly used for touch screen panels, and there are three types of glass: soda lime silicate glass, high aluminosilicate glass, and lithium aluminosilicate glass. The cover glass improves its own strength through ion exchange to achieve the purpose of glass strengthening, and the impact resistance and surface hardness of the glass after ion exchange are significantly improved.
Orifice pull-down method
The orifice down-draw method is to introduce the molten glass into the orifice drain plate groove made of platinum alloy, and the glass liquid flows out under the action of gravity, and then it is rolled by rollers and solidified in the cooling chamber.
The size of the orifice and the down-drawing speed determine the thickness of the glass, and the temperature distribution determines the flatness of the glass. The orifice plays a very important role in this process.
Whether its size is stable or not is related to key indicators such as whether the glass thickness is uniform and the surface is flat. However, due to external forces, the orifice may be deformed, and the yield will fluctuate. In addition, because the glass surface is in contact with the notch and the roller, the flatness will also be affected. Therefore, the orifice pull-down method also requires post-stage polishing.
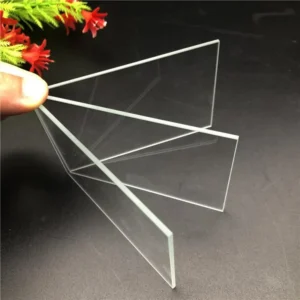
Float
The float glass manufacturing process is the most widely used flat glass manufacturing process.
This method is to transfer the molten glass to the groove filled with molten liquid tin. Using the density difference between tin and glass, it will be naturally flattened under the surface tension and gravity of the glass liquid, and then stretched to form. Quantity, adjust the operating parameters to control the thickness of the glass plate, the thickness can reach 0.3 mm.
The advantage of the float method lies in its high production capacity, easy expansion of the size of the glass substrate, and lower cost than other processes; however, the float process is used to produce TFT substrate glass, which requires further processing such as grinding and polishing in the later stage, and the cost of post-processing is high. offset some of the cost advantages. The float method was mainly used for TN/STN glass substrates in the past. Later, Asahi Glass successfully used the float method to manufacture alkali-free glass substrates, becoming a representative of the float method for manufacturing TFT glass substrates.
Flat drawing process
This process can produce thin glass with a thickness of 0.6 to 1.1 mm, and only a small amount of original glass can be used as a flat panel display substrate.
The surface quality of the thin glass produced is not comparable to that of the float method, but due to its low production cost, there are still some manufacturers using this process.
3 Types of ultra-thin float glass products
TN/STN-LCD, TFT-LCD, cover glass and other substrate glass can be produced by float process.
3.1 TN/STN-LCD glass substrate
TN/STN-LCD substrates are generally alkali-containing soda-lime-silicon ultra-thin flat glass, which is produced by float process. In order to meet the forming needs of ultra-thin float glass, the key to the production of ultra-thin float glass is to reasonably select and use tin bath forming auxiliary equipment and optimize forming control.
3.1.1 Production process characteristics
(1) Reasonable use of edge pulling machine
As one of the main forming equipments of float glass, the edge pulling machine plays an important role in throttling, thinning and controlling the direction of the original plate in the production of ultra-thin glass. Reasonably select the position of the 1# edge pulling machine, the distance between the edge pulling machines, the speed distribution, the angle distribution, and the pressing depth of the machine head, and control the strict symmetry of each parameter of the edge pulling machine, so as to reduce the lateral shrinkage of the glass ribbon and realize the step-by-step drawing of the glass. It is very important to ensure the stability of the operation of the ultra-thin glass ribbon and the smooth progress of the forming process.
(2) Using a linear motor
A linear motor is installed in the high-temperature area to increase the lateral flow of tin liquid, reduce the lateral temperature difference of the glass ribbon, and form a uniform temperature field, which is conducive to flattening and polishing of the glass liquid and improving the glass surface and optical quality; a closed slag removal device is installed at the outlet end, Remove tin slag in time to reduce tin sticking and scratches.
(3) Use of furrows
The high-temperature tin liquid flows downstream, and the cooler tin liquid flows back upstream, and the hot and cold streams meet in the thinning area, so that the micro-areas on the glass surface are unevenly cold and hot. Cooperate with the graphite sill, use the sill on both sides of the middle temperature zone of the tin bath to effectively block the impact of the backflow of cold tin liquid on the glass forming quality.
(4) Use of specific coolers
Adding a special cooler can adjust the lateral cooling strength of the cooler, adjust the lateral temperature difference of the glass plate, and also reasonably adjust the temperature in the tank. Control the water pressure and temperature of the cooling water to prevent the temperature system in the tank from changing due to excessive fluctuations.
If it is too large, the temperature regime in the tank will change.
3.1.2 Performance characteristics
(1) Composition: most of them are soda-lime-silica glass, the composition is similar to ordinary float glass
(2) Glass defects: surface scratches, defects, tin sticking and other defects are smaller than a few microns; internal bubbles and inclusions are as small as 25% of the pixel size.
(3) Surface flatness: the glass substrate for TN-LCD is less than 0.25 mm/20 mm; the glass substrate for STN-LCD is less than 0.05 mm/20 mm; at the same time, the shape processing accuracy of the substrate is required to have an error of ≤0.01 mm.
(4) Glass transmittance requirements: the transmittance in the visible light region is greater than 90%.
3.2 TFT-LCD glass substrate
TFT-LCD glass substrate is alkali-free borosilicate ultra-thin glass, although the process flow is not much different from traditional float glass, including batching, melting, forming, thermal processing, cold processing and other processes. However, the clarification homogenization and forming process technology of TFT-LCD glass substrate production is quite different from the traditional float method.
3.2.1 Production process characteristics
(1) Ingredients
The production process of TFT-LCD glass substrates has strict requirements on ingredients, mainly in the following aspects: high accuracy of ingredients; strict control of iron content; strict control of alkali metals; layered control of batch materials; moisture absorption control of batch materials.
(2) melting
From the composition of TFT-LCD glass, it can be seen that the difficulties in its melting mainly lie in the high melting temperature, serious boron volatilization, and difficult clarification. At present, the various advanced technologies of glass melting pool furnaces are mainly oxy-fuel combustion technology, electric boosting technology, platinum channel clarification and homogenization and advanced control technology.
(3) Forming
The difficulty of TFT-LCD glass forming technology is mainly high glass viscosity and surface tension, and uniform forming thickness is the key point in glass production.
(4) cold working
Due to the infiltration of tin on the lower surface of the glass during the production of TFT-LCD glass substrates by the float process, it is necessary to grind and polish the tin-infiltrated surface of the glass, which is an important feature of the float process.
3.2.2 Performance characteristics
(1) The glass does not contain alkali. TFT-LCD substrate glass belongs to alkali-free aluminoborosilicate glass. The substrate glass basically does not contain alkali metal oxides. The maximum mass percentage of alkali metal oxides in the glass is generally controlled below 0.1%. The subsequent processing of glass requires a temperature treatment of 500-600 °C. If the glass component contains alkali metal oxides (such as Li2O, Na2O, K2O, etc.), alkali metal ions will precipitate from the substrate glass and diffuse into the deposited semiconductor material when heated. , to poison the liquid crystal and thin film transistors in the semiconductor layer, among which Na+ has the highest mobility and the most serious pollution.
(2) Appropriate coefficient of thermal expansion. During the TFT-LCD manufacturing process, the thermal expansion coefficient of the TFT-LCD substrate glass must match the polysilicon and amorphous silicon thin film materials in the thin film transistor array to offset the thermal stress caused by the thermal expansion of the glass. The optimal value of thermal expansion coefficient of TFT-LCD substrate glass is 30×10-7/℃~33×10-7/℃.
(3) High dimensional accuracy. The process of manufacturing TFT-LCD includes many times of precision photolithography, so the processing accuracy of the substrate glass is required to be within 0.1 mm in terms of dimensions and even the edge, and the most important thing is to be strict with the quality of the surface flatness and thickness of the substrate glass Requirements, these dimensional accuracy will directly affect the electric field and pixels, making the grayscale and color of the display uneven.
(4) High thermal stability. Thermal stability includes two aspects of heat resistance and heat shrinkage.
Heat resistance refers to the highest temperature that the TFT-LCD substrate glass material can withstand. The strain point temperature of the TFT-LCD substrate glass needs to be greater than 650 °C to ensure the stability of the high-temperature processing of the glass during the TFT-LCD panel manufacturing process. Heat shrinkage mainly means that the substrate glass should have high temperature thermal processability and geometric stability of forming during the manufacturing process of TFT-LCD, especially to ensure that the shrinkage of the glass in the rapid cooling state is small. With the increase in size and high definition of TFT-LCD products, it becomes more and more important to control the heat shrinkage of substrate glass. Generally, the flat glass drawn directly from the quenching of the molten glass must be annealed, and a good annealing process can reduce the heat shrinkage to less than one millionth.
(5) Good chemical corrosion resistance. In the TFT-LCD production process, the substrate glass needs to be cleaned and etched by various strong acid and strong alkali chemical solutions, and finally various patterns are formed, including buffered hydrofluoric acid solution (BHF, Buffered Hydrofluoric Acid) with a concentration of about 10%. , In order to avoid the precipitation of components in the glass and various etching solutions to cause visible residues on the display or interfere with film deposition, the substrate glass must have good chemical corrosion resistance.
(6) Few surface and internal defects. TFT-LCD substrate glass requires good surface and internal quality, and internal bubbles and other glass defects should be smaller than a few microns, so as not to damage the circuit and affect the quality of the display image. If the defect on the glass surface of the substrate (scratches, scratches, surface unevenness, dust pollution, etc.) is greater than 25 mm, it will cause circuit breakage, poor adhesion of the film, resulting in product scrap or performance degradation, so there should be no stones , stripes, bubbles, scratches and other defects.
(7) Lightweight and high strength. Since the thickness of the substrate glass is only 0.3-0.7 mm, the strength requirements for such an ultra-thin glass are also high. In order to reduce the total weight of the display and reduce the sag of the glass, the substrate glass should have as low a density and as possible Possibly high Young’s modulus. It is generally required that the density of the substrate glass is ≤2.55 g/cm3, and the elastic modulus of the substrate glass is ≥70 GPa.
The above properties of TFT-LCD substrate glass are mainly determined by the chemical composition of alkali-free aluminoborosilicate glass. With the continuous development and improvement of glass chemical composition, the performance of TFT-LCD substrate glass has also been greatly improved. improvement of. Table 4 lists the chemical composition and physical and chemical properties of several typical commercial TFT-LCD substrate glasses produced by four companies including Corning of the United States, Asahi Glass of Japan, NEC Glass and AvanStrate, a joint venture between the United States and Japan.
In order to improve the strength of the glass, the ion exchange method is used to chemically strengthen the glass, forming a layer of compressive stress (CS) and a large ion exchange layer depth (DOL) on the glass surface, which can effectively improve the mechanical strength of the glass and make the glass The chance of surface scratches and drop damage is greatly reduced.
The following three types of cover glass can be produced by using the float process.
(1) Soda lime silicate glass. Its production process is the same as that of TN/STN-LCD glass substrate. Soda lime silicate glass is chemically strengthened with limited ion exchange depth and poor strengthening effect, and is generally used for low-end touch screens.
(2) High alumina silicate glass. Add Al2O3 to the glass composition to obtain high elastic modulus and Vickers hardness. In addition, Al2O3 has a large channel effect in the glass network, which greatly increases the ion exchange depth of glass chemical strengthening, and can obtain greater CS and DOL. High-aluminosilicate glass has the same characteristics as TFT-LCD glass substrates during production, with high surface tension and high viscosity; the glass melting temperature and the difficulty of clarifying and homogenizing will be greatly increased. The higher the Al2O3 content, the better the mechanical properties of the glass after strengthening, but the melting point of Al2O3 is as high as 2045 °C, which has a significant effect on the viscosity of the glass. Based on the current industrial melting conditions and capabilities, the Al2O3 content should be controlled below 24%, which can take into account and coordinate glass melting. Temperature, melting quality, forming temperature, glass crystallization, glass mechanical strength and chemical stability and other related physical and chemical properties and process properties.
(3) Lithium aluminum silicate glass. The introduction of Li2O can reduce the viscosity of the glass and make up for the difficulty of production caused by the high content of Al2O3; it can also create conditions for the secondary ion exchange, the depth of the ion exchange layer is greater, the impact strength is better, and the safety of glass self-explosion is also greatly improved. , mainly used in high-end display products. However, the introduction of Li2O makes the crystallization tendency of glass serious during production, and controlling glass crystallization is a major problem in the production of this kind of glass; in addition, the aggravation of Li2O’s erosion of refractory materials is also a prominent problem.