1. Definition, application scope and characteristics of electronic glass
Electronic glass is generally considered to be a high-tech glass product used in the fields of electronics, microelectronics and optoelectronics. It has functions such as optoelectronics, thermoelectricity, acousto-optic and magneto-optic. Key glass materials in other fields, such as photoelectric electronic glass, cover glass and display electronic glass. Compared with ordinary glass, electronic glass has obvious differences in physical properties, such as thinner thickness, greater compressive strength, and smaller thermal expansion.
Electronic glass contains a relatively rich variety, but the current development of technology and applications is mainly reflected in the display glass and protective cover glass of terminal display products such as mobile phones, tablet computers, LCD TVs, and industrial control screens. Therefore, electronic glass in the report refers to display glass. Glass (glass substrate) and protective cover glass.
The classification of electronic glass is based on chemical classification: it is divided into alkali glass and non-alkali glass: the glass with alkali metal content greater than 0.1% is alkali glass, mainly including soda lime glass (Na2O-CaO-Al2O3) and high aluminum silicate Salt glass (RO-Al2O3-SiO2, R is alkali metal); glass with alkali metal content less than 0.1% is alkali-free glass, mainly including aluminosilicate glass (Al2O3-SiO2) and borosilicate glass (B2O3-Al2O3- SiO2).
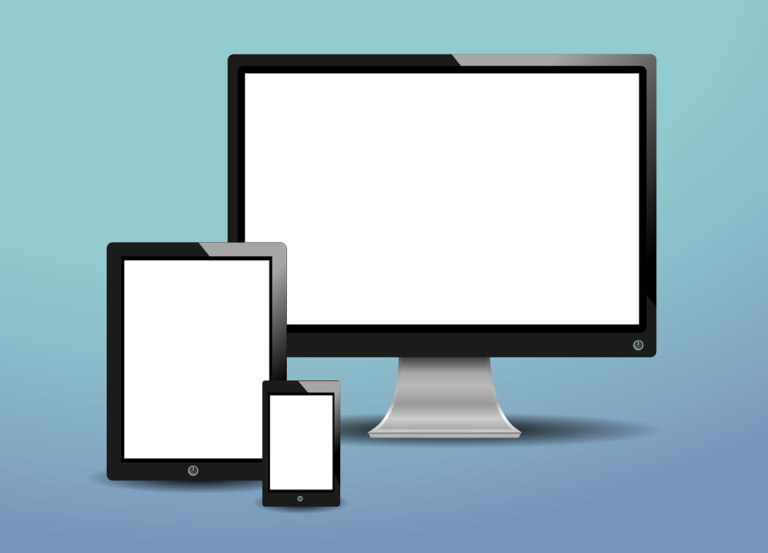
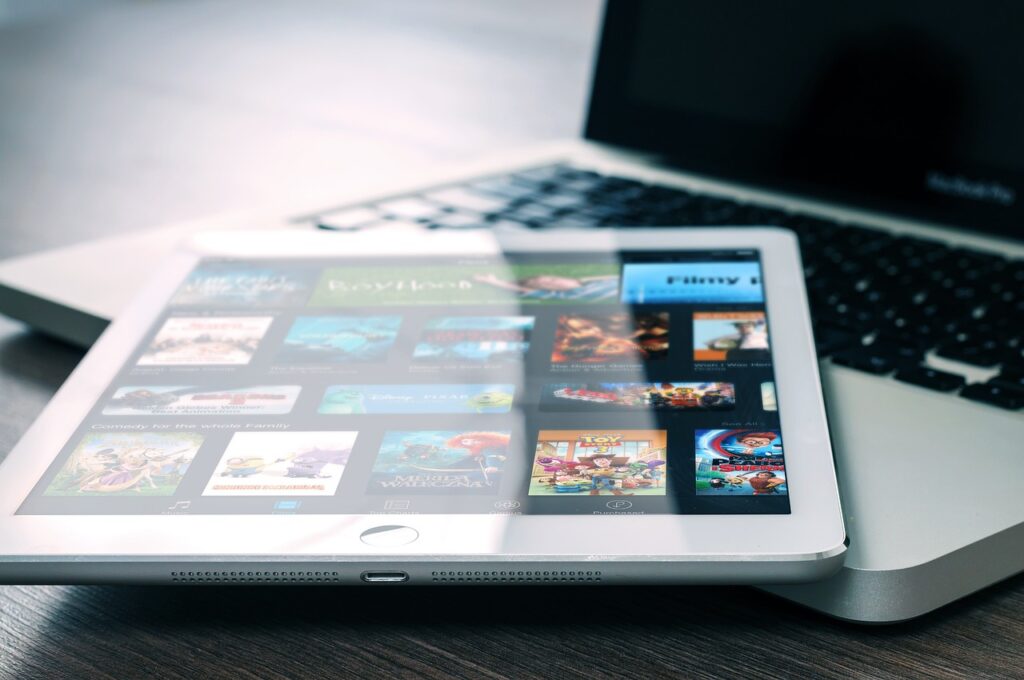
2. According to the functional use: divided into cover glass and panel glass
Panel glass substrate: mainly used as the substrate of liquid crystal or transistor, and related circuits and processes are processed on the glass surface. Among them, the glass substrate of TN-LCD and STN-LCD panels can use alkali glass, and TFT-LCD panels can only use alkali-free glass, because alkali metal ions will affect the stability of the gate voltage of thin film transistors and affect normal use. Since TFT-LCD display technology has become mainstream, glass substrates usually refer to TFT-LCD glass substrates.
Cover glass substrate: As the outermost layer of the touch screen, it plays a role in protecting the touch, and can carry out silk screen patterns, logos, etc. on the surface. It usually has the characteristics of high hardness, scratch resistance and anti-fingerprint. Alkali glass is usually used for the cover plate, and high-aluminosilicate glass has higher strength than soda-lime glass, and is widely used in high-end cover glass.
3. According to the size of the original film, it can be divided into high-generation glass and low-generation glass. Among them, the 8.5th generation and above are called the high-generation, and the 6th generation and below are called the low-generation. High-generation production line glass is larger in size than low-generation production line glass, so the output is larger, the production efficiency is higher, and the technology is relatively more mature and advanced. Glass needs to be cut in the post-production process, and the highest cutting efficiency of glass is usually around 6-8 pieces. Therefore, high-generation glass is usually used for large-size LCD TVs, and high-generation glass substrates can also be cut at high cutting efficiency. For relatively small size products, the production efficiency is improved.
4. According to the manufacturing process: divided into overflow method, float method, orifice pull-down method
Among them, the float process is the most widely used and has high production capacity, but the grinding and polishing procedure increases the process cost; the orifice pull-down process requires double-sided grinding and polishing, and the product defect rate is high, so it is gradually eliminated; the overflow manufacturing process has the best processing quality. It is more difficult and is currently the mainstream process for glass substrate processing.
The overflow method is to introduce the molten glass into the conduit, flow down the overflow tank with the bottom opening, and merge and overflow at the bottom to form a sheet-like substrate. The overflow method has the advantages of good glass surface quality, no forming medium, no secondary processing, and high yield, but the single-line production capacity is small, and there are patent barriers established by Corning Corporation of the United States. The float process is the most widely used and oldest glass forming process. After the molten glass comes out of the furnace, it flows into the groove filled with liquid tin. Due to the density difference between tin and glass, the glass in the groove depends on surface tension and gravity on the liquid metal surface. Flatten freely, and then enter the cooling chamber to cool and form. There is a certain gap between the quality and yield of float forming glass and the overflow down-drawing method. The problem of tin penetration on the surface of the glass plate can easily lead to warping and deformation of the glass product, requiring secondary treatment, which increases additional costs. However, the production capacity of float glass is large, and domestic enterprises generally have a certain amount of technology accumulation, and the technology is relatively mature.
Introduction of TFT-LCD glass substrate
In terms of flatness and roughness, the glass substrate needs to ensure that the thickness difference within the length of 20mm is less than 10nm; the strain point temperature exceeds 650°C, so as to ensure that the glass itself will not produce permanent deformation under the condition of high melting point; the glass substrate is 0.5mm In order to ensure sufficient hardness under the left and right thickness, the Young’s modulus exceeds 70GPa. The production process of TFT-LCD glass substrate is complicated, and the manufacturing environment such as plant purification is strict, which belongs to a typical high-tech industry.
Under the high-performance requirements of glass substrates, the industry naturally has technical barriers, which are mainly reflected in three aspects: formula preparation, equipment research and development, and manufacturing technology.
First, the barriers to formulation preparation. The selection and ratio of various raw materials in the glass substrate formula have a direct impact on the performance,
However, this material formula has been blocked by foreign patents, and independent research and development requires thousands of experiments to determine the appropriate ratio;
Second, barriers to equipment research and development. High-quality glass substrates are mostly processed by the overflow method, but the production equipment is independently developed by glass manufacturers and is not sold externally. Potential entrants in the industry need to redesign and manufacture production equipment;
Third, the barriers to production technology. When using the overflow method to manufacture glass substrates, it is necessary to accurately control multiple parameters such as temperature and flow rate, which is difficult to implement.
In addition to technical barriers, the glass substrate industry also has high capital barriers. The production of glass substrates is divided into the front-end melting and forming process and the back-end cutting process. The core of high-generation glass substrate production technology lies in the front-end process, which is mainly mastered by American and Japanese companies. Chinese companies can only establish back-end processing through joint ventures. Production line. The investment of a high-generation glass substrate production line is as high as 2 billion to 3 billion yuan, and the investment recovery period is as long as 5-8 years, establishing high capital barriers.
3. Introduction of the glass cover
The cover glass plays the role of protecting the outermost layer of the touch screen. It needs to have strong impact resistance and scratch resistance. Its technical barriers mainly exist in two aspects: the glass production process and the chemical strengthening process.
glass production process
Cover glass is divided into soda-lime glass and high-alumina glass according to chemical composition, among which high-alumina glass has higher Al2O3 content and has higher drop resistance. However, because the formula contains more alumina and calcium oxide, the surface tension of the glass is greater under the same temperature conditions, which is prone to warping in the later process and reduces the quality of the glass. The high-alumina glass cover plate adopts the overflow process to have a higher product yield; the use of the float process needs to solve melting control, waviness and flatness control, etc.
chemical strengthening process
The strength of cover glass can be further enhanced by chemical strengthening process, including high temperature strengthening type and low temperature strengthening type, low
Temperature strengthens more. Low-temperature strengthening refers to the use of large-radius ions to exchange small-radius ions on the glass surface below the glass transition temperature, which will cause congestion on the glass surface, thereby generating compressive stress and improving the strength of the glass.
Cover glass secondary enhanced ion exchange process:
Secondary reinforcement is the key to technological breakthroughs. The current mainstream process is one-step strengthening, which enhances the compressive stress on the glass surface, but the ion exchange depth (DOL) is low. Some glass manufacturers are able to achieve two-step strengthening. In the case of increasing the surface stress of the glass, they can also obtain a greater ion exchange depth, so that the internal cracks stop expanding at the depth when a collision occurs, and the product’s anti-drop and anti-drop performance It has been greatly improved and has become a field of competition for many glass manufacturers.
Chemical strengthening requires long-term research and development and has technical barriers. The performance of the cover glass after two-step strengthening is related to glass components, ion exchange molten salt composition, ion exchange time and temperature, etc. It needs continuous research and development to determine the chemical strengthening temperature, strengthening time and molten salt ratio. , both the first-step strengthening process and the second-step strengthening process have three variable factors that need to be systematically matched and optimized to obtain reasonable process parameters.